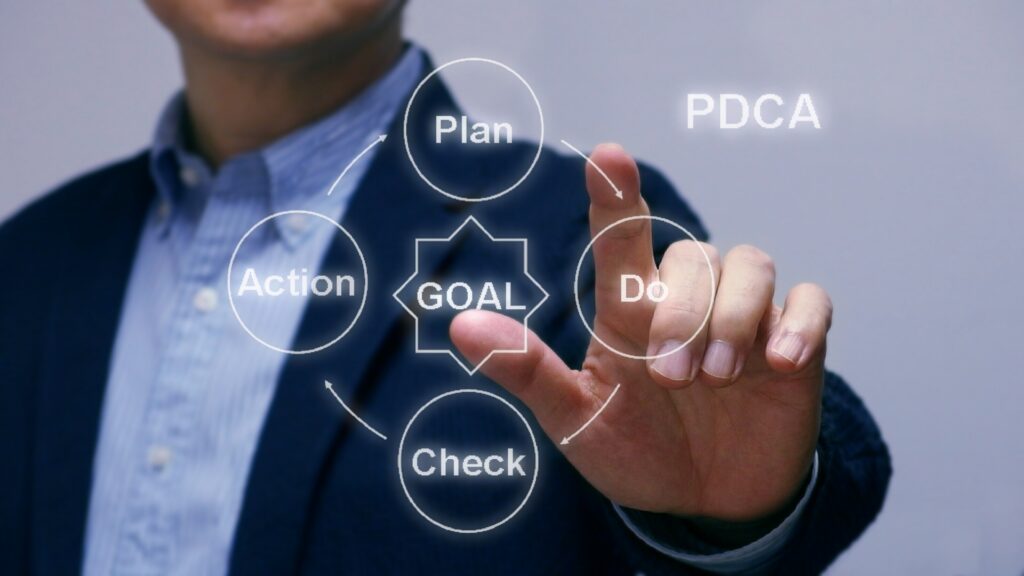
工場で、改善活動をしているのに、何故か利益に直結しないと悩んだ事が無いでしょうか?
実は、必ずしも改善が利益に直結をするとは限りません。利益を得るための改善にはいくつかのポイントがあります。
効果のある改善ポイント3選
改善活動というと、”やりやすい部分から行う”,”簡単なものから行う”というのが、結構一般的ではないでしょうか。実は、改善に成功しない、利益に繋がらないといった、理由に改善ポイントの選び方に問題があります。ここでは、成果につながる必3つの改善ポイントについてまとめてみました。
売上げを上げる
“売上げを上げる”と聞くと当たり前だろうと思われます。実はその当たり前が大事となっております。またこのセクションでは、売上げよりも利益を優先した仕事作りが必要です。
利益率が高い商品の注文を受ける
当たり前と言われれば、そうですが、まずは自社の工場ではどんな商品が実際利益率が高いのかを、製品別損益を利用して調べてそのような類似商品を積極的に注文に繋げる事です。何でも注文に繋げるのでは無く、自社にマッチしている注文を積極的につなげる事が利益UPに繋がるのです。
限界利益商品の注文を受ける
限界利益とは、現在の仕事量で社内の経費が十分にまかなえている状態で、人件費などの負担なしに商品の製造が出来るもので、材料費以外の原価がすべて利益となるものです。顧客側としては、安価で提供してもらえる、工場側としては、余った作業時間の有効活用が出来、利益を確保することでWINWINとなる方法です。
ただ、注意が必要なのは、限界利益として対応が出来るのは、工場によって異なるが、売上げ全体の5~10%程度という事と、顧客に対してその価格帯が当たり前と思われないようにする事が大事です。
Webを使って新規の顧客を開拓する。
何故Web集客で、利益が上がるのか。多分不思議に思うかもしれませんが、事実です。これは営業スタイルの違いになります。
自らが営業活動をする場合、顧客への御用聞きになりますが、同じような立場の工場が顧客に営業活動をするため価格的に安価になりやすい。一方でWeb集客のように顧客が積極的に製造工場を探している場合は、競合となる工場が少ないまたはいない場合があるため、注文に繋がった工場としては、メリットが高いつのり利益率が高くなりやすいのです。
人件費を圧縮する。
工場経営している人件費は支払うべき経費の中では圧倒的に多い費用ですので、圧縮する事で、利益に大きな影響があります。
人員スケジュールをたてる。
工場の生産スケジュールをつくる時に、どちらかというと製品の生産スケジュールを中心に生産計画をたてる事が多いと思いますが、社員の数をもとに生産計画をたてる事が重要です。このようにするとリソースの無駄が無くなり、残業を発生させない計画作りが可能です。
部署毎の管理から工場全体での管理に変える
工場などの組織では、特定の生産部門が忙しくて残業をしているのに、他の生産部署は仕事が無くて場合によっては半休をしているなんて事があるのですが、これは生産部署毎に人員管理をしている事が多いですが、人員は工場全体で管理をする事で大幅に人件費を減らす事が出来ます。
仕掛かり在庫を減らす
以外かもしれませんが、仕掛かり在庫を減らす事が人件費の削減に繋がります。現場従業員の手待ち時間が増えると、先食いや在庫を作ろうとする動きが出ますが、これは作業をする必要の無い無駄なものなのです。
経費を下げる
材料費を下げる
材料費を下げる事の基本としては、購入するのは必要量のみで余分なものを購入する事がない事が大事です。ようするに無駄な材料を購入しないという事です。毎月使うから、よく使うから、まとめ買いすれば割安だからといって数ヶ月分の材料を購入しないと言う事です。
以前であれば、車業界の仕事をすれば、2~5年は継続する事がありましたが、現在は長期間継続すると考えてはいけません。計画が長期であっても突然生産計画が止まる事もあるため、材料のまとめ買いを行うと材料が余ってしまう事があります。これは大きな損失でもあり、廃棄するにもお金がかかってしまう。
だから無駄な買い物をしない事が、材料費を抑える一番の方法なのです。
良品率を上げる事や段取りで消費してしまう材料の使用量を抑えるのも材料費を抑えるポイントになります。
⇒詳細は工場経営者必見!! 材料費を下げるためのマル秘テクニック
電気代を下げる
電機代は仕分け上は水道光熱費等で会社工場に寄って異なりますが、工場経営に取って大きな支払い額になる経費ではないでしょうか。契約状態によって異なりますが、やり方によって減らす事が可能なものでもあります。
いくつかの方法がありますが、まず過去1年間の電気使用量を管理する事です。電気使用量を管理して、最大使用量を下げる事で、基本料金を抑え、請求金額を下げる事が可能です。また、初期投資はかかりますが、工場の建物自体の断熱対策も電気代を下げるのに有効です。
産業廃棄物の費用を抑える
産業廃棄物の廃却については、費用だけでは無く、産業廃棄物管理表(マニフェスト)等の管理や各都道府県の健康福祉センターへの定期報告(これについては報告義務違反をしている企業は多いかと思います。)など管理項目も増えるため、なるべく減らすべきです。
産廃費用を減らすためには、一番必要なのは3R(リデュース、リユース、リサイクル)を実践する事です。分別をする事で、産廃費用を10分の1以下に抑える事も可能です。
まとめ
これらの改善ポイントは、ごく一部ですが、工場に取って、利益を得るための改善ポイントになります。
工場の改善はやれば良いという事ではありません。やはり工数をかけて改善活動を実施するのであれば、結果つまり利益に繋がる改善ポイントを選びましょう。
工場(会社)の目的は利益を稼ぐ事です。利益を意識する事は重要です。意識しなければ、効果的な改善ポイントを見つける事も出来ません。正しい改善ポイントに力を入れる事で、たった一カ所を改善する事で、数百万、数千万単位の効果を生む事もあります。
「工場の未来のためのレポート「利益に繋がる9つの改善ポイント」
- 無料
- 無償で提供します。
工場の改善活動は普段行っている事でしょう。
・しかし改善活動は成功しても利益に繋がらない
・そう悩んだ事はありませんでしょうか?
・実は利益を得るための改善にはテクニックが必要なんです。
・今回、利益に繋がる改善ポイントをレポートにしました。
・そんなレポートを提供します。
クリックを押してレポートをダウンロードしてください。
参考資料
工場改善の第一歩 人件費を下げるために従業員を雇いましょう。