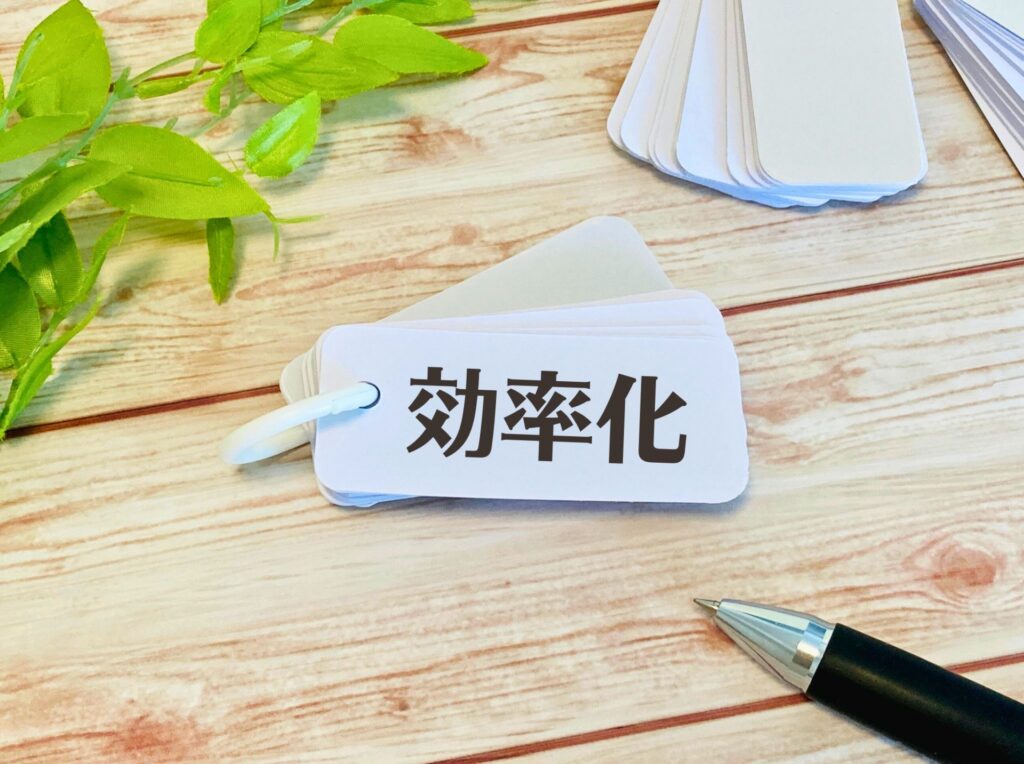
工場にとって改善活動は必要不可欠なものです。現在のビジネスにおいて、工場の効率化と改善はこの競争社会において重要な要素となています。成功する工場はこの成功する改善方法に焦点を絞った、効果的な戦略を行っておりますので、具体的な事例を紹介していきたいと思います。
リーン生産手法の導入
工場の生産効率化する方法としてリーン生産方式があります。
リーン生産方式は、米国マサチューセッツ工科大学のジェームズ・P・ウォマックらが1990年に日本のトヨタが行っている生産方式(TPS:Toyota Production System、以下TPS)を参考に体系化させたもので、必要な時に必要のものを必要なだけ作る(JIT)を行いムリ、ムダ、ムラを無くし、生産性を向上する方法になります。因みにリーン(lean)とは脂身のない赤身の肉の事をいい、リーン生産方式は、贅肉の取れた生産方法と呼ばれるものです。
日本国内では、もともとトヨタ自動車の改善方法であるTPSが浸透している事もあるため、リード生産方式を知らない人も多いかと思いますが、日本の工場であれば、TPSをよく知っている工場も多いかと思いますので、その場合は、リード生産方式を学ぶ必要はありません。中身は同じだからです。ただ、TPSを知らないのであれば、リード生産方式は体系化しているため、学びやすいかと思います。
具体的には、工場や工程全体を観察する事で問題点を発見してそれを現場を初め関係者を巻き込んで、改善を行う方法でトヨタが行っていた工程の効率化を行う事が出来ます。それにより工程の最適化をする事ができます。
テクノロジーの活用
工場の効率化においては、最新テクノロジーの導入が重要かつ必須です。それは自動化やIoT機器の導入です。
ロボットの導入による自動化は、タスク作業のバラツキ防止や効率化を図る事が出来ます。また自動化は作業時間が大きく変わる事で、人員削減にも高い効果を発揮します。
ここで注意が必要なのは、無計画で自動化をする事は効率化に繋がらない場合もあります。それは自動化する場合は、必ずボトルネックにターゲットを絞る必要があるということを知っておいて下さい。
一方でIoTデバイスの導入については、生産ラインのモニタリングを実施する事で、リアルタイムに生産の状況や問題点を検知する事が出来ます。それによって、問題点に対して、リアルタイムに対処出来るようになります。また、従業員などが書く日報などもデジタル化する事で、データーの解析が出来ます。それらによって工程の現状を分析する事で、リアルタイムな対応が出来ます。
IoTデバイスや日報のデジタル化は一見すると効果が無いように感じるかもしれませんが、現場の状況を把握する事で、改善のポイントを知る事が出来る重要な事例となります。これがビックデーターとして活用できるかは経営者の考え方次第です。
データ分析と予測メンテナンス
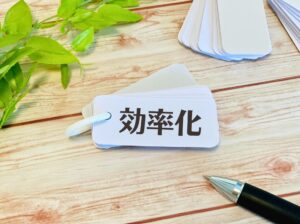
工程から取得したビックデーターの分析をする事で、工場の効率化がを図る事が出来ます。
ビックデーターをAI(人工知能)によって分析する事で、工場全体での生産性の最適化を図る事が可能となります。全体最適化は、理論で判っていても、人が手計算で行うには限界があります。その為、AI(人工知能)を利用する必要があるのです。
それによって各リソース(設備:Machine、従業員:man)の最適化により、残業の削減、生産スピードのアップ、レスポンス向上になり、最終的には原価低減になり生産性の向上につながります。
また設備の状態をリアルタイムで観察する事で、最適なメンテナンス頻度を算出する事で、稼働率を最大化する事で、生産性を向上に寄与する事ができます。
人材育成と参加型マネジメント
効果的な改善には、従業員の積極的な参加が欠かせません。古来より日本の企業では、従業員が積極的に改善提案を行い、実行される参加型マネージメントを行う事で成功を収めています。
従業員自らが仕事に責任を持ち積極的に改善に参加する事で、工場の効率化が実現できます。
ただ、ここで重要なのは、従業員だけで改善を行うのでは無く、経営者が必ず改善活動に参加する必要があります。それは改善活動には、全体最適化と部分最適化があり、従業員には自らが行おうとしている改善活動が、全体最適化なのか、部分最適化なのかを判断する事は非常に困難です。
改善活動は、全体最適化でなければ、生産性の向上には繋がりません。つまり、改善活動をしても、工場や会社の利益には繋がらないのです。そのため、経営者が、その是非を判断する必要があるのです。
部分最適化は一見やった感はあるかと思いますが、現場の自己満足で終わってしまう可能性がありますので、経営者は製品別損益のような指標を用意をする必要があります。
サプライチェーンの最適化
工場の効率化を図る事で、サプライヤーチェーン全体も最適化が可能になります。工場内が最適化する事で、外部に影響を及ぼす事が可能になります。
ここで良い例として、自動車業界との取引でよく見聞きする、カンバンと三発と呼ばれるものがあります。”かんばん”はある意味正規の注文書で納品の1~2日前にしか出ません。つまり事前に生産をしていなければ、納期通りに納品をする事が出来ません。そこで利用されるのが三発と呼ばれている内示情報です。基本保証はありませんが、3ヶ月先の生産予定の情報を知らせてもらう制度ですが、これによって工場全体の生産計画をたてることが可能となります。
3ヶ月先の情報で、材料の発注予定を決めたり、2ヶ月先の予定で、生産計画の立案、人員計画の立案をする事が出来ます。例えば人員計画をたてる事で、人が足りない事が判明した場合、それが長期なのか短期なのかで判断が変わりますが、短期であれば、残業を予定したり、長期になる見込みで、月に140時間以上の稼働時間が見込める場合は従業員の採用活動をしたり、場合によっては、派遣会社に事前にオファーをしたりといった計画を組む事が可能となります。
自社工場も内示情報をもとに、このような計画を組む事が可能になるため、自社内の統制が取れた段階で、同様の情報をサプライヤーに対しても提供する事で、サプライヤー自身も生産計画を組みやすくなります。
中長期の生産計画をサプライヤーに提供する事で、生産の効率化が図れる事で、納期の短縮やコスト協力にも積極的になる可能性があります。そしてサプライヤーとの良好な関係性も構築する事が出来るでしょう。
これは仕入れ商品だけでは無く、物流関係のサプライヤーにも言える事で、中長期の情報を提供する事が、関係性向上に寄与する事でしょう。
まとめ
今回、工場の効率化を図るための、5つの事例をご紹介いたしました、如何だったでしょうか。
工場経営者にとって、生産性の効率化は必須事項です。ただ改善活動を続ければ結果が出るという事ではありません。これからの改善は結果に繋がるかを経営者として見極める事が重要と考える必要があります。
今回ご紹介した事例は、ひとつひとつが、生産性向上に繋がる方法です。また、これらの対策事例は、すべて関連性があるものですので最終的はすべての項目をコンプリートする必要があります。
ひとつ言える事は、過去の経験だけで、生産性を上げるのでは無く、最新のテクノロジーを利用する必要があり、どの部分を優先させるかを経営者は常に考える必要があります。
また、工場の生産効率化戦略を成功するためには、競争力を維持するためには、持続的で適切な改善戦略を選択する事が必要となっていきます。
「工場の未来のためのレポート「利益に繋がる9つの改善ポイント」
- 無料
- 無償で提供します。
工場の改善活動は普段行っている事でしょう。
・しかし改善活動は成功しても利益に繋がらない
・そう悩んだ事はありませんでしょうか?
・実は利益を得るための改善にはテクニックが必要なんです。
・今回、利益に繋がる改善ポイントをレポートにしました。
・そんなレポートを提供します。
クリックを押してレポートをダウンロードしてください。
参考資料
工場の改善提案・ネタ・アイデアの事例!改善提案が思いつかないときの解決策もご紹介!