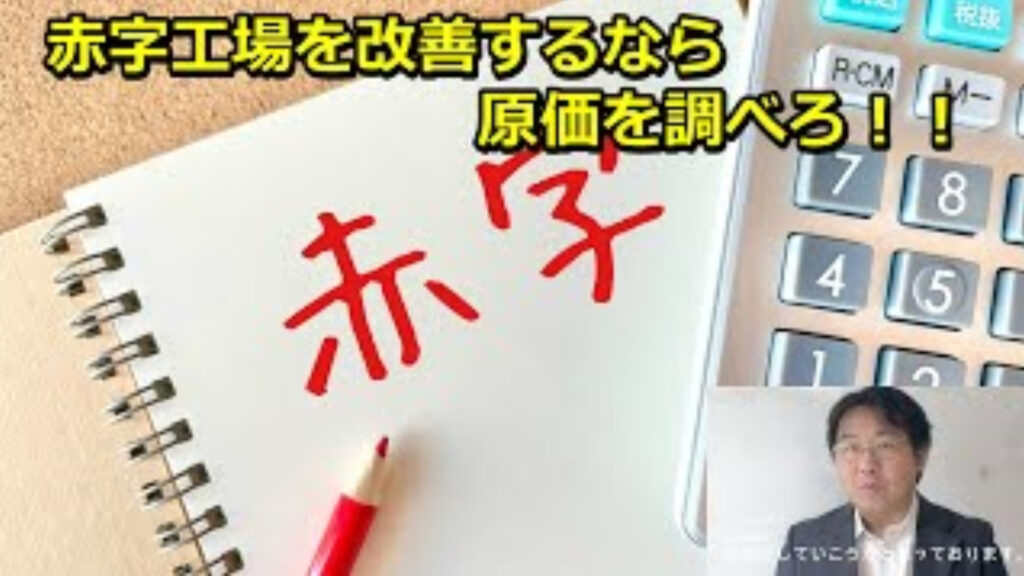
赤字工場を改善するなら原価を調べろ
工場が赤字なった時に経営者のあなたであれば、何を行うでしょうか?
赤字の原因は、不良の垂れ流し?
私が工場長に就任した当時、工場は赤字でした。
工場は忙しく残業も多く、一方で不良が発生している事で、納期遅れが発生する事が多々ありました。
そのため、誰もが、不良問題を解決すれば、赤字解消に繋がると思っていました。当の自分自身もそうでした。
だからこそ、技術出身である自分自身が、品質改善に陣頭指揮を執って、徐々にであるが、品質改善には繋がっていき、結果世間並みレベルまで品質改善には成功しました。
しかし、赤字の解消には至らなかったのです。「何かがおかしい」
私は、改善の度に指標として、管理部門から、原価明細を要求していました。どう原価が変化しているのかをチェックするため、しかし、このデーターに大きな変化は無い。通常不良率の改善による原価の変化は大きくなければならないのに逆に原価の変化は小さいのです。
この時に私は違和感を覚えました。
本当に赤字の原因が不良だったんだろうかと、
そのため、原価の計算方法について、メスを入れる事にしました。当時原価計算は、管理部門が、手元にあるデーターをもとにして、生産している製品毎に計算をしていましたが、原価計算をするに対して、拾ってくるデーターが圧倒的に足りていなかった、そして足りないデーターを補完するために、つじつま合わせのような原価計算をしていた事が判明したのです。
当時の管理部門の担当者は、以前の経営者たちから、この原価計算の仕方を教育されていましたので、本人は悪くは無かったのですが、財布を預かる部門なんでこの違和感をもっと感じて欲しかったと当時は思っていました。
実は、計算式を考えた、私の前任者たちが残したものは、とても大きな負の遺産だったという事が判明するのでした。
工場の原価を見直す。
原価算出に問題あり!?
工場の実際の原価を算出するのは、実は結構難しいです。
特に、無形材料や人件費などは、配分次第で、商品毎の原価が大きく変化してしまうからです。
我々の工場も塗料や樹脂材料を取り扱っていましたので、多くの無形材料が存在していました。そのため現場毎の消費量報告は欠かせないはずでしたが、実際現場から管理部門への消費量の報告がされていなかった事が判明しました。
つまり、どの商品にどのくらいの材料が消費されているか判らずに、材料の受発注をしていた事になります。そのため材料の過不足はかなり発生していました。これは人件費も同様です。
当然でてくる原価計算もアンマッチとなるはずでした。
これらの原因は私の前任者たちが残した大きな負の遺産でした。
まあ嘆いてもしかたないので、原価計算の見直しをする事としました。
原価を計算するためには、現場の実際データーが必要
原価計算に必要なのは、実際のデーターです。
当時現場では、日報を書く習慣かありましたが、日報は、現場管理者がまとめて保管するだけでした。もちろん異常値がでれば、その記録を見ての議論等はありましたが、それまででした。
実際、現場にあった、日報には、各作業者毎に、作業時間や材料の消費量など記録されていました。ただ、その細かな情報は、管理部門には伝わっていない事がわかりました。
そこで行ったのが、日報のデーター化です。今の言葉で言えば、DX(Digital Transformation)化では無いでしょうか。
現場で書いた日報を現場管理者にPCにデーターを打ち込んでいく事を行ってもらいました。かなりブーイングがありましたが、かなり強制的に行いました。(現在であれば、タブレットを利用したりすれば、利便性はアップするかと思います。)作業時間が増える等の文句はすべて黙殺しました。(まあかなり酷いですね、でも必要な事でした。)
これによってアナログだったデーターをデジタルデーターにする事で、集計、解析が可能になりました。
実際私自身も、集計プログラムを作りました。最初はExcelベースのものでしたが、結局データーベースを構築しないといけなかったのを覚えています。
ここで抽出したかったデーターは大きく3つでした。商品毎の作業時間、材料消費量、直行率(入荷から出荷までの良品率)これらのデーターを使う事で、はじめて商品毎の原価を弾く事が出来たのです。
そして驚くべき結果が出ました。
ここで、判明したのが、特定の商品が原価割れもいいところで、予定原価の10倍もの材料を消費しているものがあったのです。正直これには、自分でも驚きを隠せませんでした。
原価を正しく集計しなければ、判らなかった事でした。
そしてその原価の問題が、1台の機械に集約をされている事が判明したのです。将来的な改善は必要と考えていた部分ではありましたが、緊急性が高いとは想定外でした。
その機械を調査した結果、様々な問題がさらに判り、結局設備の総入れ替えを決断をしました。入れ替えには紆余曲折がありましたが、入れ替えた事で、原価が25分の1と急降下しました。
そしてそれによって黒字化に成功したのです。
原価を知らなければ経営判断は出来ない。
こごて、言っている原価とは、実原価の事です。
私が使用している、実原価は、非常にシンプルです。
1.材料費
2.直接労務費
3.在庫費用
この3つのデーターです。もちろん売上げは当然加味されますが、
生産高(売上げ+在庫の増減) |
材料費(仕入れ-在庫の増減) |
労務費 |
管理費 |
指標の中心は、売上げで無く、生産高です。工場の場合当月内で材料の購入、生産、出荷が終わらない事が多く数ヶ月に工程がまたぐ事があるため、このような指標を使用します。そのため生産高は、当月の生産した価値を表しています。また、材料費も仕入れ額から在庫の増減を引くことで、当月に消費したものを表します。これを商品毎に行います。
また労務費は、商品毎の作業時間をもとにして、按分する事で、割り当てます。商品あたりのコストがはじけますし、実際従業品数に対して、仕事が多いのか少ないのかも判明します。
何故こんな、指標を使用しているかというと、生産高と材料費、生産高と労務費の割合は、同じ商品であればほぼ一定となります。そのため想定外の問題がおきないかぎり、予想通りの結果になります。そのため購入する材料の量や、用意すべき現場作業者の人数を想定する事が可能となるのです。
まとめ
原価管理は、工場の運営には必要不可欠です。
正しく原価を把握する事は、様々な経営判断を迅速に行う事が可能となってきます。
昔であれば、集計が大変だとかもあるかもしれませんが、テクノロジーの時代ですので、PCレベルで出来る管理であれば、積極的に原価の把握に取り組む事が、最短の経営判断が出来るほか、最適の結果を目指す事に繋がる事と思います。
もし、赤字であれば、目の前の火を消す事に注力をするのでは無く、おちついて火事の原因を原価を調べる事で探し出す事から行う事が近道です。
参考資料
赤字工場が3ヵ月で粗利5倍アップ! 業績が驚異的に伸びた理由とは?
工場経営者必見!!工場の利益に直結する影響度の高い改善ポイント 3選